Transforming control rooms: How technology enhances efficiency in manufacturing
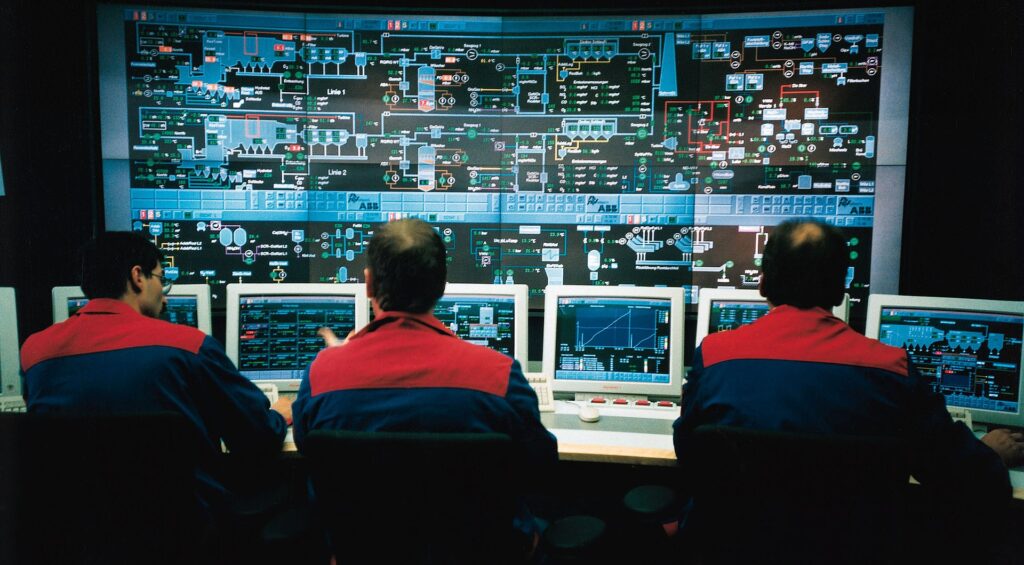
German solid waste incinerator. By Steag, Germany – Steag, Germany, CC BY-SA 3.0
As the central intelligence hub of the manufacturing process, the control room is the brain of the organization. When investing in technology to make the process more efficient (i.e., smarter), it is a logical place to start. Control rooms have made a major technological leap in recent years, transforming from on-site, reactive, and highly stressful spaces into professional, digital, and highly flexible environments that proactively avoid potential issues.
Although they tended to look spectacular, with lots of screens or even flashing lights, traditional process control rooms were straightforward environments with limited possibilities. Operators monitored and controlled the manufacturing process on-site, based on limited sensor data. Anomalies were typically met with high stress, as it often took time to identify the root cause of the issue.
This vision contrasts with that of their modern counterparts. While the screens are still in place, all information is now digitally available and can easily be distributed to any location. This means the control room could be located 100 miles away and even control multiple production plants.
Alternatively, multiple small control rooms can handle day-to-day decisions, with a central crisis room managing escalations. Any configuration is possible, which makes contemporary control rooms very flexible. The large amount of available real-time data also allows staff to drastically cut the time needed to pinpoint and resolve issues.
For example, in the past an alarm would be triggered when a temperature sensor exceeds a certain threshold. In most cases, a field worker would need to investigate the situation on-site. Today, a lot more information is available, allowing the control room staff to assess what’s happening from behind their desks.
Boosting Efficiency
The ultimate goal of the control room is to use predictive analytics to proactively prevent all emerging issues. While even the most sophisticated current systems cannot guarantee this, modern technology certainly plays a pivotal role in risk mitigation. This includes not only production hazards but also upholding safety protocols for workers.
It is therefore critical that operators have direct access to all the information they need. This may sound basic, but it often isn’t the case; information is often not available in the same system. Organizations may choose to separate networks — for example, placing process data on one network, internal data on another, and a third that accesses the internet. This is a nightmare for operators, who must constantly switch between computers to do their jobs. That’s why state-of-the-art systems can integrate all information into a single (virtual) environment. Although the networks are still separated, the information appears to be in the same environment (“integration at the glass”), and operators only need a single keyboard and mouse to do their jobs, resulting in a more ergonomic way of working.
Empowering the Operator
The most critical presence in the control room is always the operator. Firms need to avoid overloading staff with an abundance of data. The optimal way to present and visualize the information is important and this will not only increase efficiency it will also enhance the operator’s job satisfaction and retention.
For example, in Barco’s Global Control Room Report 2024, 91 percent of operators working in highly efficient control rooms reported job satisfaction—significantly higher than the 51 percent of satisfied workers in less efficient environments.
Smarter Systems, Reduced Risk
In the control room every component is expected to function 24/7, and even scheduled interruptions should be minimal. How can organizations achieve this always-on ideal?
The Barco report recommends investing in high-quality equipment. Control rooms are typically environments designed for the long haul, and this should be reflected in the hardware and software. Redundancy of all critical components, with seamless takeovers when the original unit fails, also helps ensure uptime.
However, not all risks are related to the system. External threats, such as hackers, can arise. Security breaches can result in weeks of downtime or millions of dollars in ransom payments. Systems should therefore be extremely secure, shielding against all possible penetration attempts.
Some organizations address this by completely isolating their critical systems (so-called “air-gapping”). However, this is not 100 percent safe and it can create a false sense of security while severely limiting system flexibility. Instead, the modern approach is to deploy a software platform that is completely secure upon installation (“secure by default”).
Transforming control rooms: How technology enhances efficiency in manufacturing
#Transforming #control #rooms #technology #enhances #efficiency #manufacturing