Heat and puff: Experiencing the art of glassblowing
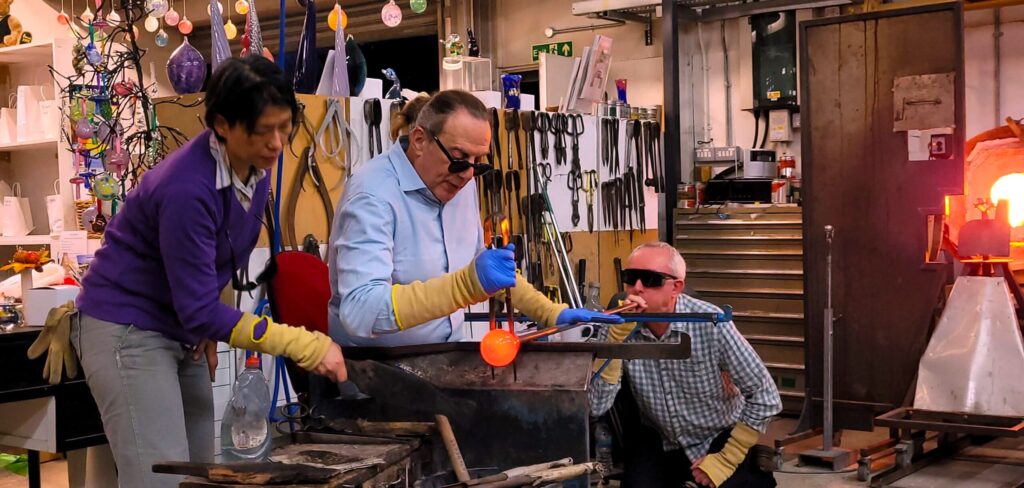
Blowing glass. Image by Tim Sandle.
Glassblowing is an ancient craft that can be used to create a variety of wondrous objects, from the functional to the purely aesthetic (glass blowing was invented in the 1st century BCE, by Syrian crafts folk).
But what is it like to actually create glass objects? Last year I tried my hand at blacksmithing, creating a poke (see the Digital Journal article ‘Hammer and tongs: What is it like to be a blacksmith for a day?’)

The next step outside of my comfort zone was to try another technique embedded in the arts and crafts movement: glassblowing.
The venue was the Adam Aaronson studio in Surrey, UK, where Aaronson specialises in free blown glass, drawing inspiration from Turner, Whistler, and Monet.

The tutorial began with selecting a design and colour scheme. I elected to produce a bowl.
The process begins when a molten ball of glass is gathered on the end of a blowpipe (hence it is called the ‘gather’). The extracted glass is very similar to honey in terms of texture.

The molten glass can have a coloured dye added to it and then short puffs of air are blown into it.

The glass is then manipulated into the desired shape using tools (jacks) and techniques like swinging, pinching, and pulling. The various tools can manipulate the molten glass into any desired shape.
There is further heating and blowing.

Glassblowing involves three furnaces. The process begins with a crucible of molten glass (“the furnace”). The second furnace is called the “glory hole”, and this is used to reheat a piece in between steps of working with it.
The final furnace is called the “lehr” and is used to slowly cool the glass, over a period of a few hours to a few days to stop it from cracking.
The blowing technique is important. This has the effect of forming an elastic skin on the interior of the glass blob that matches the exterior skin caused by the removal of heat from the furnace.
The practice of blowing down the metal tube requires the lips to be moistened. The best technique is to encase the narrow opening of the tube completely around the lips and then attempt to whistle.

The joy is as much with the experience as the end product. The possibilities are endless, and the glassblower can experiment with different colours, shapes, and textures.
Naturally, there were health and safety features to observe. The furnace is hot – very hot. The transformation of raw materials into glass takes place at around 1,320 degrees Celsius and the glass emits enough heat to appear almost white hot.

All metal needs to be considered hot (and steel does not even begin to look ‘hot’ until it is at 500 degrees Celsius). Another thing to observe is broken glass.
The experience is good fun and the end product is something beautiful to keep. Such experiences not only help to keep old traditions burning, but the challenge can help form and shape individuals too.

Digital Journal was at the Adam Aaronson Glass Studio, West Horsley, Surrey, UK.
Heat and puff: Experiencing the art of glassblowing
#Heat #puff #Experiencing #art #glassblowing