Technology vaporizes bags, yielding gases to make recycled plastics
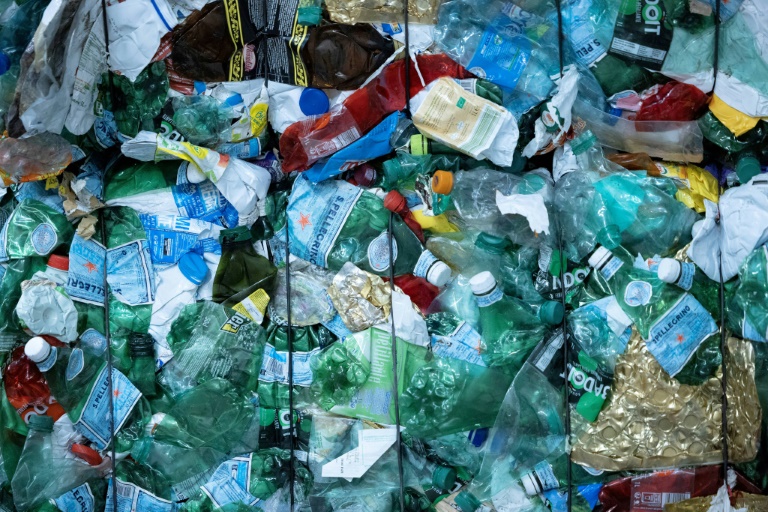
Europe produced 58.8 million tonnes of plastics in 2022 – Copyright AFP JOSH EDELSON
Researchers have developed a new process to take plastic bags, vaporise them, and then convert the extracted materials to make a new set of recycled plastics. The basis of the technology is a catalytic process that efficiently reduces polymers to chemical precursors.
The innovation from University of California – Berkeley may help to bring us closer a circular economy for plastics.
The catalytic process turns the largest component of today’s plastic waste stream, polyolefin plastic bags and bottles (polyethene, the component of most single-use plastic bags; and polypropylene, the stuff of hard plastics, from microwavable dishes to luggage), into gases — propylene and isobutylene. These gases are the building blocks of polypropylene and other types of plastics.
It is hoped that the process, if scaled up, could help bring about a circular economy for many throwaway plastics, with the plastic waste converted back into the monomers used to make polymers, thereby reducing the fossil fuels used to make new plastics.
Clear plastic water bottles made of polyethylene tetraphthalate (PET), a polyester, were designed in the 1980s to be recycled this way. But the volume of polyester plastics is minuscule compared to that of polyethylene and polypropylene plastics, referred to as polyolefins.
Polyethylene and polypropylene plastics constitute about two-thirds of post-consumer plastic waste worldwide. About 80 percent ends up in landfills, is incinerated or simply tossed into the streets, often ending up as microplastics in streams and the ocean. The rest is recycled as low-value plastic, becoming decking materials, flowerpots and sporks.
To reduce this waste, researchers have been looking for ways to turn the plastics into something more valuable, such as the monomers that are polymerized to produce new plastics. This would create a circular polymer economy for plastics, reducing the need to make new plastics from petroleum, which generates greenhouse gases.
The chemical process employed three different bespoke heavy metal catalysts: one to add a carbon-carbon double bond to the polyethylene polymer and the other two to break the chain at this double bond and repeatedly snip off a carbon atom and, with ethylene, make propylene (C3H6) molecules until the polymer disappeared. But the catalysts were dissolved in the liquid reaction and short-lived, making it hard to recover them in an active form.
In the new process, the expensive, soluble metal catalysts have been replaced by cheaper solid ones commonly used in the chemical industry for continuous flow processes that reuse the catalyst. Continuous flow processes can be scaled up to handle large volumes of material.
Studies demonstrated that a tungsten catalyst was more effective than the sodium catalyst in breaking polypropylene chains. The two types of catalyst in combination lead to an even more powerful solution.
The research has been published in the journal Science, in an article titled: “Polyolefin waste to light olefins with ethylene and base-metal heterogeneous catalysts.”
Technology vaporizes bags, yielding gases to make recycled plastics
#Technology #vaporizes #bags #yielding #gases #recycled #plastics